FAQ - Questions and answers about neodymium magnets
What is a neodymium magnet and how does it work? What are these powerful magnets used for?
Dive into the fascinating world of neodymium magnets – discover their strength, applications, and secrets! Here you will find precise answers to the questions that come up most often, clearing up any doubts how they function and what they can be used for. Understand why neodymium magnets are considered the strongest in the world and how they can make your life easier.
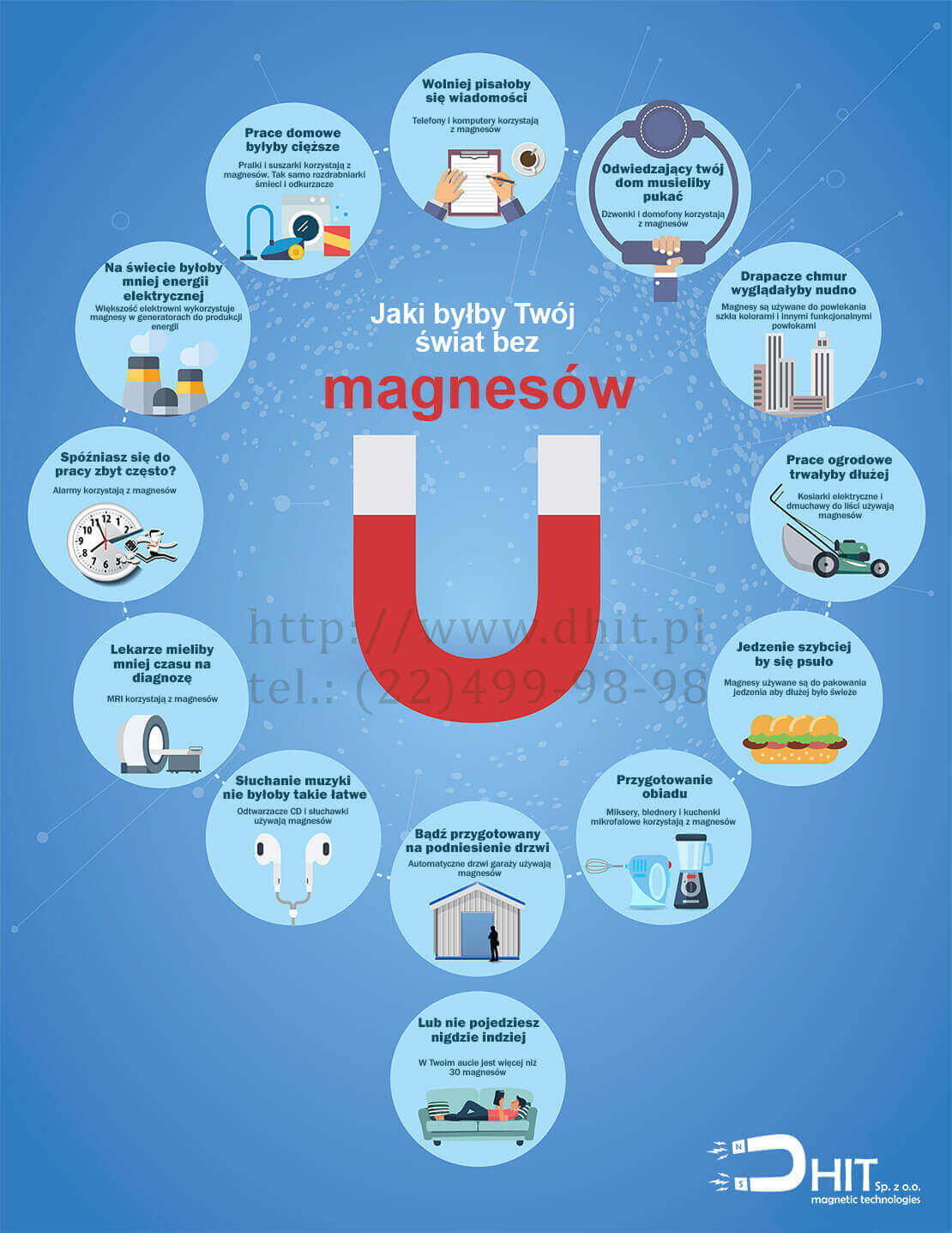
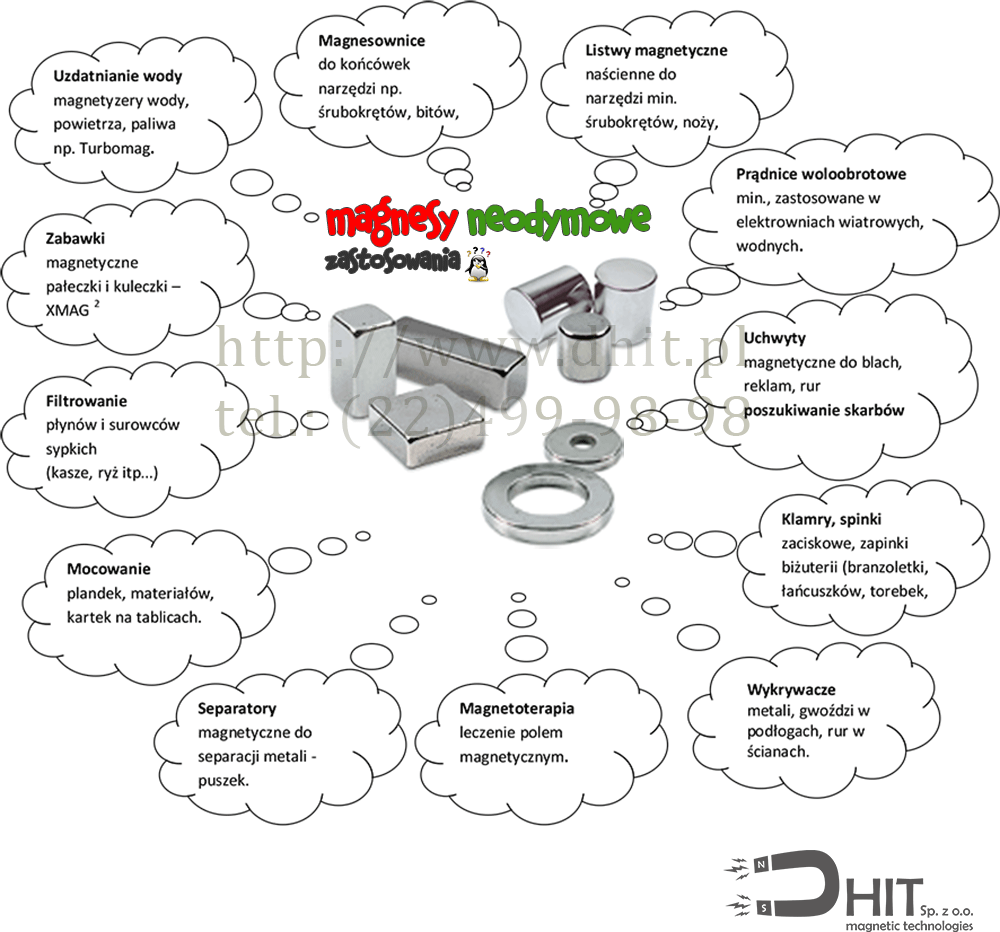
Shipping, delivery, and returns
Find answers to questions about shipping methods, costs, delivery times, and return policies. Learn how to easily manage online orders.
Working with Neodymium Magnets
Learn how to safely and effectively handle neodymium magnets – from mounting to separation and use in projects.
Typically, these magnets are available in packs where one side is covered with adhesive material on the south pole, and the other on the south pole. This allows attraction when needed, e.g., for creating closures or connectors.
Our self-adhesive magnets are made with foam glue, which is also available separately as double-sided adhesive stickers. This high-performance adhesive provides excellent shear strength, preventing shifting and lifting of edges.
To use the magnet, simply peel off the backing paper and apply it to the desired location. The adhesive is strong enough to allow repositioning of the magnet for precise fitting. After placing the magnet, press it firmly to ensure even adhesion.
We recommend waiting 24-48 hours after attaching the magnet for the adhesive to fully cure before applying any force to the bond.
Key features:
Extremely strong magnetic force, allowing effective attraction even from a distance.
Compact sizes, meaning even small magnets have great power.
High resistance to demagnetization under normal usage conditions.
Wide range of applications, from industrial to everyday use at home.
However, they require caution during use to avoid damage or injury.
Application tips:
Always read the instructions for the glue you are using.
Before applying the glue, make sure the surfaces are clean. Residues, grease, or dirt can create a barrier that prevents proper adhesion of the magnet.
It is recommended to sand smooth magnet surfaces to improve glue adhesion.
Gluing magnets to plastic can be more difficult due to issues with achieving proper glue adhesion. Consult the glue manufacturer's technical support for advice on plastics.
The best choice of glue is two-component epoxy resin, which works well in most cases. Recommended glues include: Loctite Plastic Bonder Epoxy, E6000 Adhesive, Super Glue, Gorilla Glue, and many others.
Avoid using hot glue guns as the high temperature can demagnetize the magnets.
Use a smartphone app: There are apps that help identify the poles of a magnet.
Use a teslameter: A teslameter measures magnetic induction and shows which pole is which.
Magnetic pole detector: You can also purchase a pole detection device that will help you easily identify the poles. For more information on magnetic directions, visit NS magnets.
Using a strong neodymium magnet: Place the magnet next to a strong neodymium magnet, ensuring the poles of the magnets touch.
With a flow of electricity: Connect the magnet to electrical wires, which causes the current to induce a magnetic field.
With a specialized device: Magnetic induction devices available in electronics stores allow you to magnetize a magnet using a strong magnetic field.
Important: Magnetizing a neodymium magnet can be difficult if the magnet is damaged or distorted. More information on magnetization methods and pole directions can be found in our technical guide.
A magnetic holder is a magnet with an enclosed casing that protects it from damage, such as cracks or scratches. Thanks to its special design, the magnetic holder may include additional features like threads or handles, making installation and use easier. The benefit of magnetic holders is their stronger attraction, but they have a smaller range of action. For more information about magnets and magnetic holders, visit technology.
Another method is the PDR technique (Paintless Dent Repair), which involves bending the sheet using a special kit (cost approx. 500 PLN). This time-consuming method allows for dent removal without the need for repainting.
Alternatively, a PDR 1000 device can be used, which generates a magnetic field and is dedicated to removing dents from flexible steel bodies. This solution is fast and professional, and is perfect for automotive workshops. For more information about magnets, visit our technology guide.
Start by shifting one magnet to the side, instead of dragging it directly. Hold the magnets to prevent them from sudden connection. Details available on the separation tools page.
Magnet Applications
Explore inspiration and examples of using neodymium magnets in the home, industry, and creative projects.
Types of magnets:
Neodymium magnets: the strongest on the market, ideal for advanced applications.
Ferrite magnets: an economical solution for less demanding projects.
Rubberized magnets: resistant to damage and suitable for delicate surfaces.
Specialist magnets: for sensors, magnetic separators, or holders.
Magnets in various shapes: cylinders, cubes, rings, and custom forms upon request.
Examples of applications:
Home: Tool organization, photo mounting, or creating magnetic closures.
Office: Magnetic boards, document holders, organizers.
Industry: Metal separation, mounting components, electric motors.
Education: Physics experiments, teaching magnetism principles.
Hobbies and art: Creating decorative magnets, modeling, DIY projects.
Magnet UMP 67x28 [M8+M10] F120 GOLD, ideal for work with kids,
Magnet UMP 75x25 [M10x3] F200 GOLD, a universal choice with a 290 kg lift,
Magnet UMP 94x28 [M10] F300 GOLD, for more demanding tasks.
For more information, visit the what magnet for searching page.
Technical information about magnets
Detailed technical data on neodymium magnets – from grades and protective coatings to their properties and applications.
Basic principles:
Opposite poles (N and S) attract, creating a stable connection.
Like poles (N and N or S and S) repel, making it difficult to bring them together.
The force of interaction depends on the distance between the poles and the power of the magnets.
Magnetic fields can affect conductors as well as some electronic devices, so caution is advised.
Proper utilization of magnetic poles enables effective applications in technologies such as electric motors and separators.
In America powerful neodymium magnets were produced in the plants of GM using a method of dynamic temperature reduction of molten isotropic powder. Why the combination of neodymium with iron and boron yielded much better results? The use of neodymium was considerably cheaper than samarium, and additionally neodymium is characterized by much better magnetic parameters. Unfortunately its Curie temperature was decidedly too low, which is why it was decided to increase that temperature to 530°C. Such a value was obtained by adding a boron additive to the composition of the neodymium magnet. Moreover it is also possible to adjust the magnetic properties of the magnet by introducing additional constituents, like gallium Ga, copper Cu, niobium Nb plus aluminium Al.
Nano-crystalline magnetic material was developed, composed of grains with a size smaller than 100 nm. The grains that were discovered nano-crystalline, in unlike monocrystals are separated by much larger boundaries with much greater surface magnetic power as well as a less ordered internal structure. Thanks to the use of, at the stage of production elements from the group of rare earth metals along with with the addition of iron, they are characterized by high remanence value. Such excellent magnetic parameters also result from one more thing, that is the coupling of magnetic moments of neodymium and iron. This enables excellent magnetization neodymium-based magnets.
The manufacturing neodymium-based magnets is based on two technologies. In Japan use a method of sintering powders of ferromagnetic materials, while in the USA fast cooling has become popular. Depending needs and expectations, neodymium-based magnets can also be produced through the use of other alloys, such as copper, aluminum, or gallium. Thanks to such additives it is possible to modify magnetic properties itself, its strength level, as well as resistance to high temperatures. It is possible to make the magnet highly resistant to harmful atmospheric conditions, for example water, which can cause rusting of iron. On the other hand continuous enhancement of powder metallurgy has contributed to developing various kinds of alloys, which greatly influenced the increase of the so-called. Made in a modern way a neodymium magnet, can achieve a magnetization level exceeding 1.6T, meaning much higher for example the magnetic field emitted by Earth.
Neodymium magnets can be made as sinters, but it is also possible to produce neodymium magnets as so-called bonded magnets, using resins or plastics as a binder.
The magnetic flux density is the amount of magnetic flux per unit area. While the flux density will become slightly stronger when two magnets are placed vertically on top of each other, since the surface area remains the same, there will be no significant difference. For example, if two magnets of size MW 10mm x 10mm are placed on top of each other, the magnetic flux density will be almost the same as for a single magnet of size MW 10x10 mm.
Key points:
Magnesium is paramagnetic, meaning it reacts to a magnetic field, but the force of attraction is very weak.
Under normal conditions, magnets do not noticeably attract magnesium, as its paramagnetic properties are insufficient to create a significant force.
To observe the paramagnetism effect of magnesium, a very strong magnetic field and specialized equipment are needed.
Magnesium differs from materials like iron, cobalt, and nickel, which are ferromagnetic and strongly react to magnets.
Due to its properties, magnesium is used in various industries, but it is not used as a magnetic material.
Magnet manufacturing process:
Material selection: Permanent magnets are made from ferromagnetic materials such as iron, nickel, cobalt, or neodymium-iron-boron alloys (NdFeB).
Shaping: The material is shaped into the desired form through casting, sintering, or pressing magnetic powders.
Magnetization: The finished component is subjected to a strong magnetic field, which causes the magnetic domains in the material to align, giving it magnetic properties.
Finishing: Depending on the application, magnets can be further ground, coated with protective layers, or finished in other ways.
Quality control: Each magnet is tested for its magnetic properties and durability to meet user requirements.
Electromagnets: In the case of electromagnets, the process involves winding a conductor around a ferromagnetic core and connecting it to a power source.
Key facts:
Magnetic therapy is primarily used for pain relief, tissue regeneration, and improving blood circulation.
There is research indicating that low-frequency magnetic fields may support the treatment of inflammation, bone fractures, or carpal tunnel syndrome.
The effectiveness of magnetic therapy has not been scientifically proven, and expert opinions are divided.
This therapy is generally safe, but may not be suitable for individuals with pacemakers, metal implants, or during pregnancy.
Always consult with a doctor before starting magnetic field therapy, especially in the case of serious conditions.
Differences between magnets:
Magnetic strength: Neodymium magnets (NdFeB) are several times stronger than traditional ceramic or ferrite magnets.
Composition: Made from neodymium, iron, and boron, whereas traditional magnets are usually ferrite.
Size: Neodymium magnets can be very small yet extremely strong.
Application: Neodymium magnets are used in modern technologies such as electric motors, hard drives, and medical devices.
Durability: Neodymium magnets are more brittle and less resistant to high temperatures than ferrite magnets, requiring protective coatings.
Why are neodymium magnets the strongest?
High magnetic strength: They are capable of generating a very strong magnetic field, even in small sizes.
Modern technologies: Used in devices like electric motors, wind turbines, and speakers.
Compactness: Due to their strength, they can replace larger and weaker magnets.
Alternative: Another type of strong magnet is samarium-cobalt magnets (SmCo), which are more resistant to high temperatures but less common and more expensive.
More information on magnetic materials can be found on the technology page.
Remanence (Br) is the maximum magnetic induction that the magnet can retain after the magnetic field is removed. The Br value for neodymium magnets ranges from 1.1 to 1.4 T.
Coercivity (Hc) is the magnetic field required to erase the remanent magnetization. Coercivity of neodymium magnets ranges from 800 to 2000 kA/m.
Maximum energy product (BHmax) is a measure of the energy a magnet can deliver per unit volume. The maximum energy product for neodymium magnets is between 200 and 400 kJ/m3.
These parameters are measured using specialized devices such as gaussmeters, teslameters, and magnetometers. More information can be found on the technology page.
Here are density values for various magnetic materials:
Water: 1.0 (reference value)
Ferrite magnet: around 4.8
Neodymium magnet: around 7.5
Alnico magnet: around 7.3
Iron: 7.9
Neodymium magnets are heavier than other magnetic materials, making them ideal for various industrial uses such as motors and generators.
Neodymium magnets became a technological breakthrough due to their exceptional magnetism and relatively low mass compared to traditional magnets. As a result, they have found widespread use in many industries, including electronics, automotive, and medicine.
The most commonly used material for shielding is iron, which has very high magnetic permeability. Other materials, such as stainless steel, cobalt, nickel, and copper, can also act as magnetic shields, but their effectiveness is lower.
Shielding works by placing a material with high magnetic permeability between the source of the field and the protected area. Such materials create a so-called Faraday cage, which changes the direction of the magnetic field lines and reduces their effect on the protected space.
Isotropic magnets, formed without a magnetic field, can have multiple poles. Anisotropic magnets, which are formed in a strong magnetic field, can also be magnetized multipolar, but only in a determined direction.
Every magnet always has an even number of poles, which is essential for its operation.
Ferrite and samarium-cobalt magnets - from -60°C to 250°C.
Neodymium magnets - depending on the type, from -130°C to 230°C.
Alnico magnets - can withstand temperatures up to 550°C.
All magnets tolerate low temperatures well, but higher temperatures can lead to demagnetization. It is important to remember that overheating magnets can result in a loss of attraction force and demagnetization.
More information about magnetic separators can be found on the magnetic separator page.
Magnetic domains in ferromagnetic materials are small fragments where the magnetic field is directed in one constant direction. When a magnet is brought near, it strengthens the magnetic field in selected domains, causing the rest of the domains to orient in the direction of the magnet's field, making iron attracted to the magnet.
More about poles can be found on the enes magnet page.
Safety
Rules for safe use of magnets, including information on potential hazards and responsible handling of magnets.
For safety, avoid storing your phone near strong magnets. More information can be found on the dangerous magnets page.
The most important thing is to remain calm and wait for the natural process, rather than running to doctors. More information can be found on the dangerous magnets page.
Curiosities about Neodymium Magnets
Discover interesting facts about neodymium magnets – from their history to their extraordinary properties.
The advantages of neodymium magnets:
highest energy density relative to mass,
magnetic stability with a loss of 1% per decade,
cost-effective production.
Most Common User Issues
Find solutions to issues such as corrosion, loss of magnetic force, or installation difficulties.
Selection tips:
Magnetic force: Consider how much power is required for your application.
Size and shape: Ensure the magnet fits the space where it will be used.
Protective coating: Choose a magnet with a corrosion-resistant coating, such as nickel-plated.
Operating temperature: Neodymium magnets may lose their properties at high temperatures.
Application: Check if the magnet meets the requirements for industry, electronics, or household use.
In the United States, magnet fishing is generally permitted with exceptions, e.g., in South Carolina, where the law prohibits removing artifacts from state waters.
In Indiana, starting in 2025, a special permit is required for magnet fishing.
In the UK and the USA, there are regulations limiting magnet fishing with regard to removing historical artifacts.
To avoid issues, consult with local authorities before starting this activity.
Other methods include using hand tools or a lighter, heating the plastic on the protruding part, then using pliers or scissors to cut the clip off, this may damage the clothing.
If the clip is attached with adhesive tape, try scraping the tape, heating it with a hair dryer and using a cotton swab.
For more difficult security types, consult with store assistance. More information can be found on the anti-theft clips page.
First, neodymium magnets can be divided into two types: based on the design and method of securing the rope. As for securing, magnets mounted from the top are ideal for fishing from docks, bridges, or checking wells. They are also perfect for fishing from boats.
Models like DHIT Magnet GOLD come in five strengths, from 120 kg to 600 kg. On the other hand, magnets with double attachment, like DHIT Magnet GOLD, are the most versatile and allow for fishing both from above and the sides (the two handles can be screwed together at the sides for pair hunting).
As for popularity, the most commonly chosen models are: F200x2 GOLD, F300x2 GOLD, and F550x2. If you have doubts about choosing the right magnet, feel free to contact us. We are happy to advise and help you choose the model that best meets your expectations and goals.
More information about search magnets can be found on the which magnet to use for treasure hunting? or in the search magnets category.