Neodymium Magnets - Nd2Fe14B Production Technology
neodymium is the strongest known material for producing magnets
The production of sintered neodymium magnets is a process in which special alloys of neodymium and other metals are melted and sintered into the shape of a magnet. This process is highly complex and requires specialized machinery, equipment, and skilled workforce.
The first step in the production of sintered neodymium magnets is preparing the appropriate proportions of neodymium and other alloys, such as iron and boron. These alloys are then melted in a high-temperature furnace and poured into a mold, which is subsequently cooled and solidified.
After casting, the magnet undergoes heat treatment to achieve the desired hardness and strength. The next step is mechanical processing, during which the magnet is ground, aligned, and then subjected to further drying and quality control.
Upon completion of the production process, sintered neodymium magnets are ready for use in various applications, such as electric motors, audio and video equipment, as well as in the automotive and aerospace industries.
Precautionary Principles
Do not use neodymium NdFeB magnets in:
- Acidic, alkaline, organic, or dissolving environments (unless the magnet is hermetically isolated from the environment) or radioactive radiation
- Water or oil (unless the magnet is isolated from the environment or you are prepared for the magnet to lose its magnetic properties quickly)
- Electrically conductive fluid - electrolyte containing water
- An atmosphere containing hydrogen
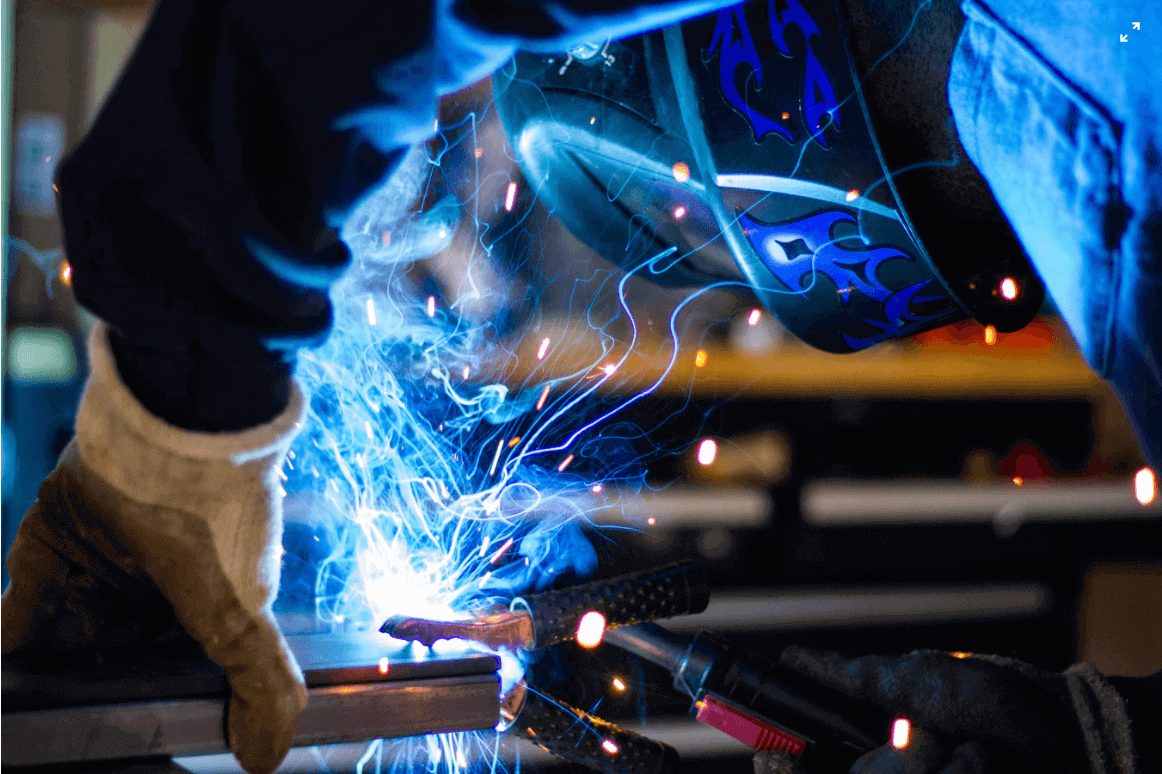
A neodymium magnet is a sintered alloy of powdered metals with a rare earth element from the lanthanide group - neodymium, discovered in 1885. After magnetization, its action is several times stronger than that of the commonly known ferrite magnet. For example, a regular ferrite magnet (such as those used in speakers) can lift a few grams of weight, while a neodymium magnet of the same size can lift ten times more. Thanks to their size and ability to operate within a relatively wide temperature range, as well as the widespread use of various mounts, neodymium magnets started gaining popularity already in the late 1980s.
Neodymium magnets are prone to corrosion in humid environments. Therefore, they are coated with a thin layer of nickel, silver, gold, gold-nickel, or epoxy. The magnetic properties of neodymium magnets (NdFeB) significantly deteriorate at temperatures exceeding 130°C and are largely dependent on the material they are made of, whether it is N-type - 80 degrees Celsius with low permanence, or, for example, M-H-SH-UH-EH types, which can operate up to 210°C. Generally, NdFeB magnets with higher permanence coefficients withstand higher temperatures without losing their magnetic properties.
Neodymium magnets (NdFeB) are about 13% lighter than SmCo (ferrite) magnets and are brittle (although not to the same extent as the latter). Therefore, any mechanical processing using diamond tools should be carried out before magnetization. Neodymium magnets can be magnetized in several ways, depending on their application.
Neodymium 60Nd - a chemical element from the f block, group 3, lanthanides, a yellow metal - is used as an additive to alloys, and its oxide is used to color glass (artificial rubies), porcelain, enamel, as well as in neodymium lasers. In the open air, it reacts coldly with oxygen, forming neodymium oxide Nd2O3, and releases hydrogen from heated water, forming neodymium hydroxide Nd(OH)3. When reacting with acids, it forms neodymium salts containing pale reddish-violet, hydrated Nd3+ cations, such as neodymium chloride NdCl3, hexahydrate neodymium nitrate Nd(NO3)3.6H2O, octahydrate neodymium sulfate Nd2(SO4)3.8H2O.
- discovery year - 1885
- atomic number - 60
- atomic mass - 144.24
- electronegativity - 1.2
- valence - +3
- melting temperature - 1020oC
- boiling point (p = 1 atm) - 3030oC
- number of known isotopes (including stable isotopes with a half-life of over 1 billion years)
- ground state electron configuration:
[Xe] 4f4 6s2
1s2 2s2 2p6 3s2 3p6 3d10 4s2 4p6 4d10 4f4 5s2 5p6 6s2
Reduced Magnetization and Demagnetization
The magnetization of magnets weakens over time, but at normal room temperature, magnetization decreases only slightly over many years. Therefore, because most people think that they never lose their magnetism, such magnets are called "permanent magnets." The magnetic force of a permanent magnet depends on the ambient temperature and changes according to the temperature coefficient. When the temperature is high, the magnetic force weakens, and when the temperature is low, the magnetic force becomes stronger. Permanent magnets cannot withstand heat when constantly heated at high temperatures, and the reduction of magnetism continues due to changes in the direction of iron atoms. Once a certain temperature is exceeded, the magnet is completely demagnetized. This temperature is called the Curie point or Curie temperature, discovered by French physicist Pierre Curie in 1895. The tips of atoms can also become disorganized due to vibrations when strong pressure is applied to a permanent magnet, which can also lead to reduced magnetization.
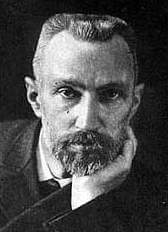
Permanent Magnets
A material that continuously generates its own magnetism is called a "magnet." Artificially produced magnets based on iron contain about 1% carbon (C) and other elements besides the main component, iron (Fe). Because the atomic magnetism of iron is attached in the same direction between other atoms, such as carbon, continuous magnetism is generated externally, and such magnets are called permanent magnets.
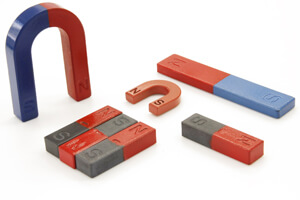
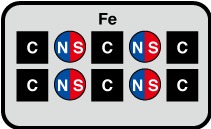
Adsorption Force
Adsorption force, also known as attraction force, refers to the force between two objects, such as a magnet and a magnetic body containing iron. Newtons (N) are used as representative units for adsorption force. Basic mass units such as kilogram-force (kgf) and pound-force (lbf) can also be used.
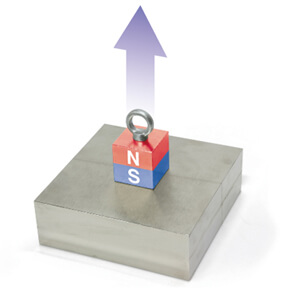
Maximal Energy Product
The maximum value of the energy product of the magnetic field (H) and the magnetic flux (B), i.e., (Bd) * (Hd), is referred to as the maximal energy product (BH-max). The maximal energy product indicates the measure for the maximum magnetic flux obtained based on the unit volume of the magnet. As this value increases, the straight line between point P and the origin (0) approaches 45 degrees, indicating good balance between the magnetic flux density (B) and the coercivity (Hcb / Hcj). The maximal energy product is denoted in kilojoules per cubic meter (kJ/m3) in the SI unit system and as Megaoersteds (MOe) in the CGS unit system.
Magnetic Flux Density (B)
An example of magnetic force is lines, and many lines represent related lines of magnetic force derived from a unit surface field. Remanence (Br) indicates the amount of magnetic flux (B) residually maintained when a permanent magnet reaches magnetization saturation to point M due to an external magnetic field (H), and then the external magnetic field (H) returns to zero. Surface magnetic flux density refers to the magnetic flux density with respect to the external surface of the magnet. Magnetic flux density is denoted as tesla (T) in the SI unit system (WB/m2) and as gauss (G) in the CGS unit system (Mx/cm2).
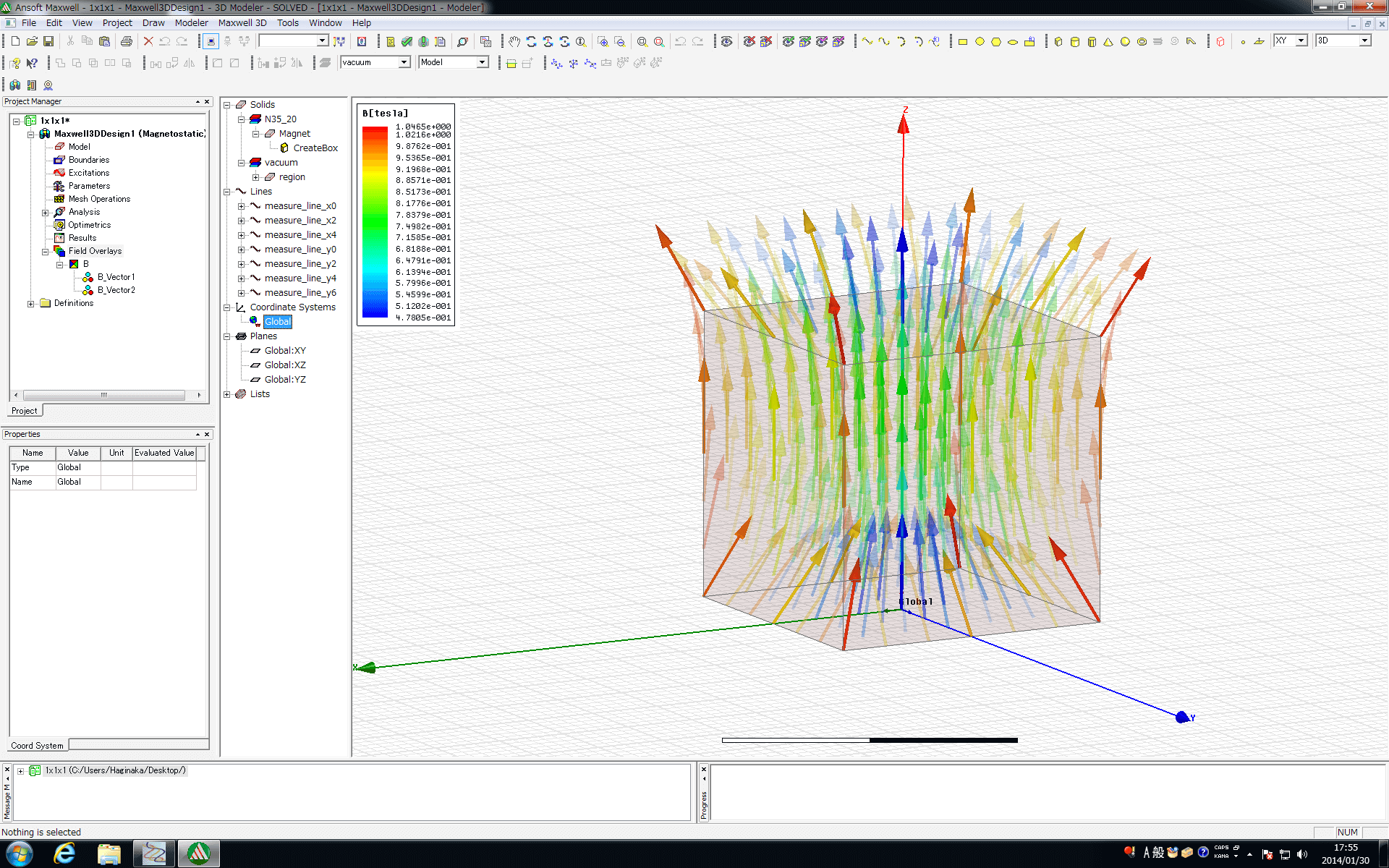
Coercivity (Hcb / Hcj)
Coercivity refers to the resistant magnetic force. Coercivity refers to the strength of the external magnetic field (H) required to restore a magnetized magnetic body to a state where it is not magnetized by an opposing (-) magnetic field (H). As this numerical value increases, the resistance to demagnetization develops, making it more difficult to decrease magnetization. Coercivity is denoted in amperes per meter (A/m) in the SI unit system and as oersteds (Oe) in the CGS unit system.
Assessment of Magnet Performance
Although the performance of a magnet is often abstractly described as "weak or strong," a third party cannot accurately assess the performance of a magnet because the sense of strength or weakness is subjective. The performance of a magnet is typically tested by conducting an evaluation based on the hysteresis curve drawn using a BH analyzer. This hysteresis curve is called the BH curve, and the main indicators derived from the tests are evaluated according to international unit standards, such as magnetic flux density (B), coercivity (Hcb/Hcj), and maximum energy product (BH-max). Information about magnetic units can be found in this magnetic unit converter.
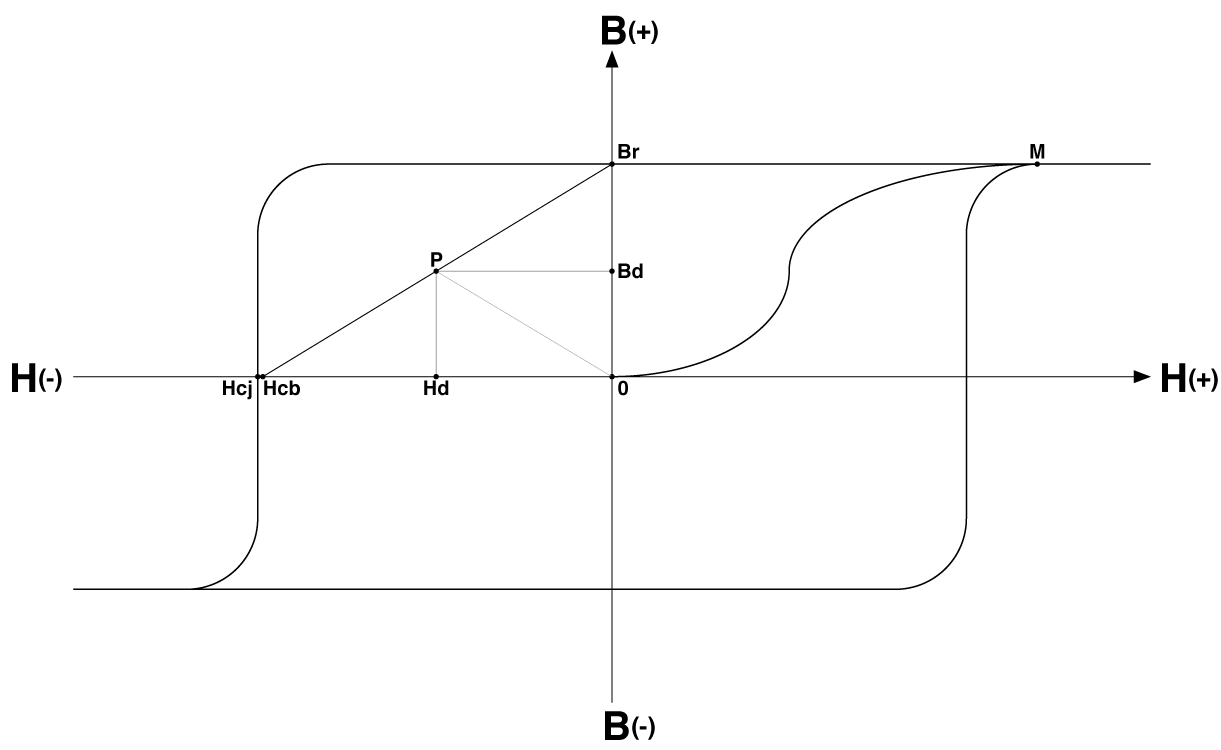
Magnetism
The ability of a permanent magnet is often referred to as "magnetic strength," but more precisely, the reactive property of a magnet is called "magnetism," the force of magnetism is called "magnetic force," and the area in which magnetism operates is called a "magnetic field" or "magnetic flux." These properties depend on the energy that is the tension of the rope between the N and S poles, as the poles repel each other and try to move away from each other according to the two-pole immobility exposed in the magnet. This magnetic energy cannot be visually observed under normal conditions. Magnetism exits from the N pole and enters the S pole, and this flow between magnetic poles is visually represented by lines called "magnetic field lines." This image allows for the visual confirmation of magnetic energy using a magnet and iron powder.
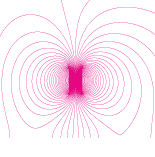
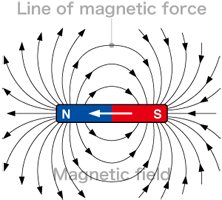
Load
Load is defined as the force generated when two points come into contact, such as between a magnet and a steel plate. The load varies with friction, surface condition, and impact. The sliding load, which indicates whether the magnet and the steel plate, etc., can remain in place without sliding, enduring horizontally applied load, is also denoted in newtons (N).
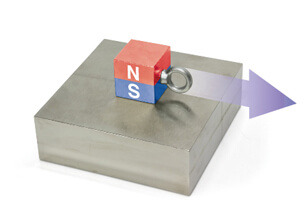
The resulting numerical values differ depending on the usage environment and measurement method. As a result, it is necessary to define the usage environment and measurement method when applying adsorption force in magnet specifications. In our laboratory, these forces are defined during measurement according to the following measurement method and usage conditions.
-
Adsorption Force
Adsorption force is the force when the magnet is pulled away from the steel plate perpendicular to the vertical axis, and the magnet separates from the steel plate.
-
Sliding Load
Sliding load is the force when the magnet is pulled parallel to the horizontal axis, and the magnet moves away from the steel plate. The force of the magnet in this orientation is much weaker compared to the adsorption force and ranges from 10% to 25% of the declared force in parallel measurement.
- The thickness (T) of the steel plate and the thickness (H) of the magnet are as stated above.
- The magnet is placed at the center of the steel plate.
- The surface area of the steel plate is at least three times (300%) larger than the surface area of the magnet.
- The material of the steel sheet is pure iron (Fe).
- The surface of the steel sheet is flat without irregularities, and the friction coefficient is not taken into account.
- Any gap between the steel plate and the magnet is closed so that there is no gap.
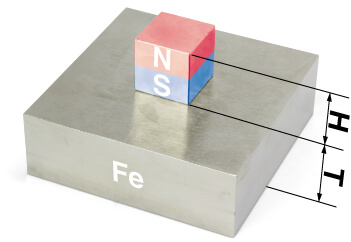
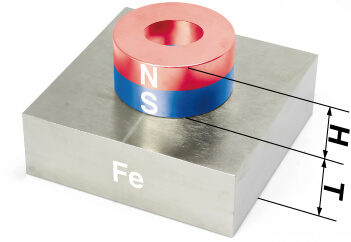
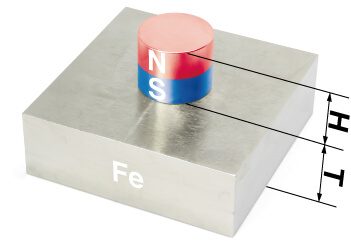
Remember! Neodymium magnets will "rust" and have a thin layer of nickel, silver, gold, gold-nickel, or epoxy (cannot work in water or oil).
Axially
Magnetized through length or thickness. The strongest points are on the flat surfaces.
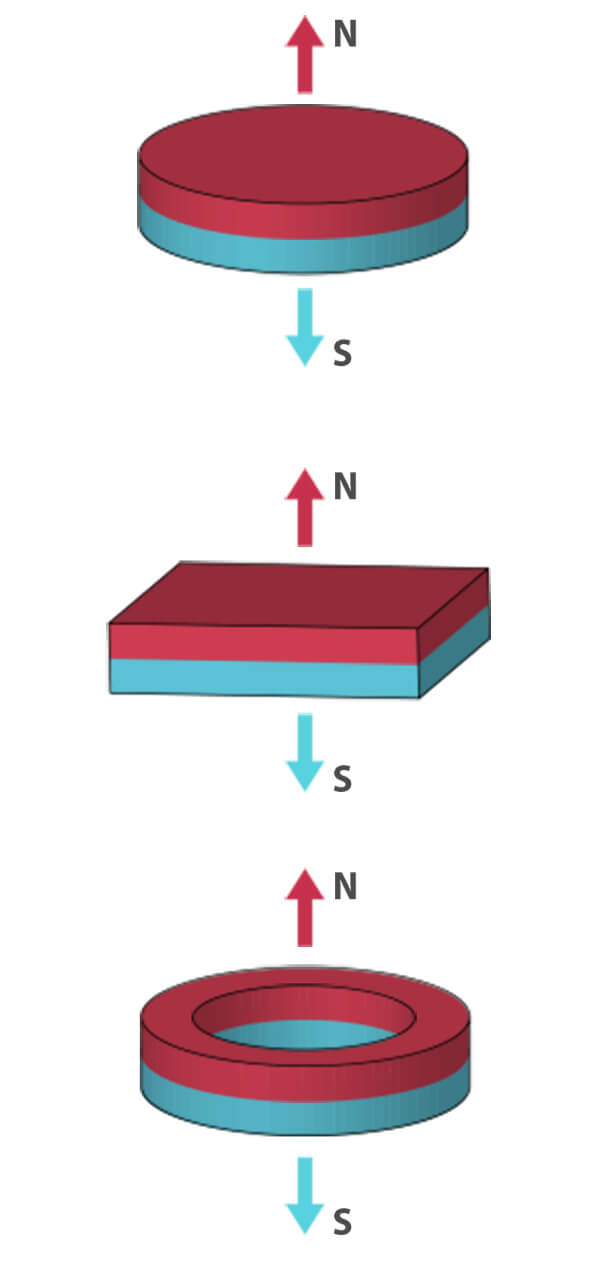
Diametrically
Magnetized through the diameter. The strongest points are on the curved surface.
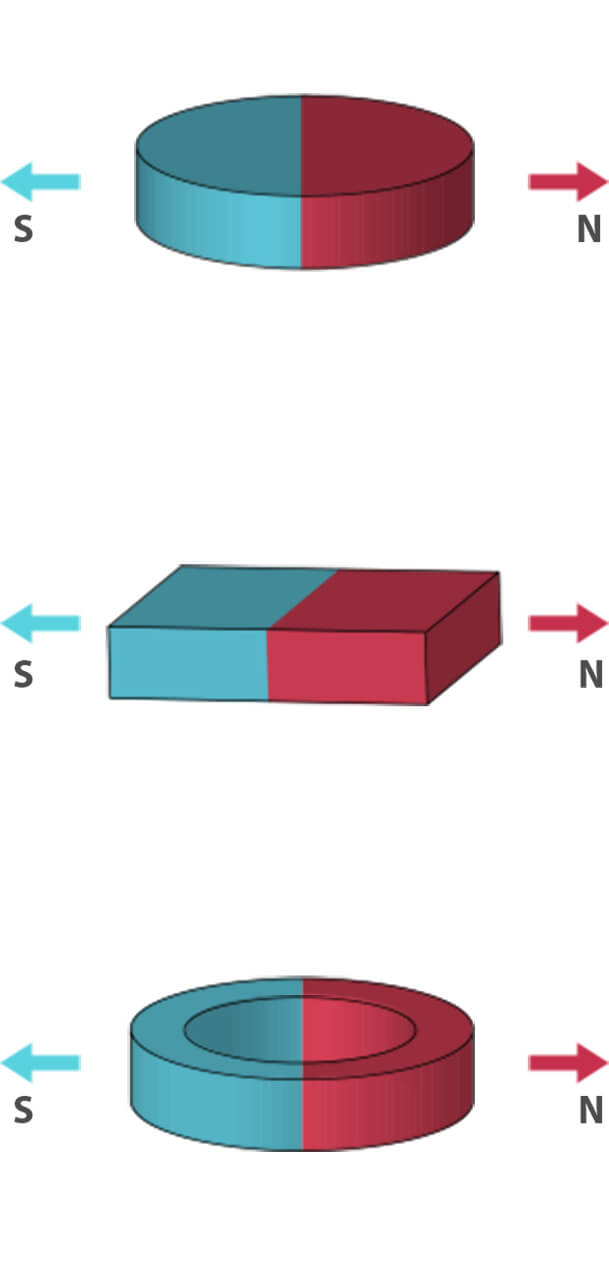
Radially
Magnetized along the diameter of the magnets. All north poles, all south poles have alternating poles.
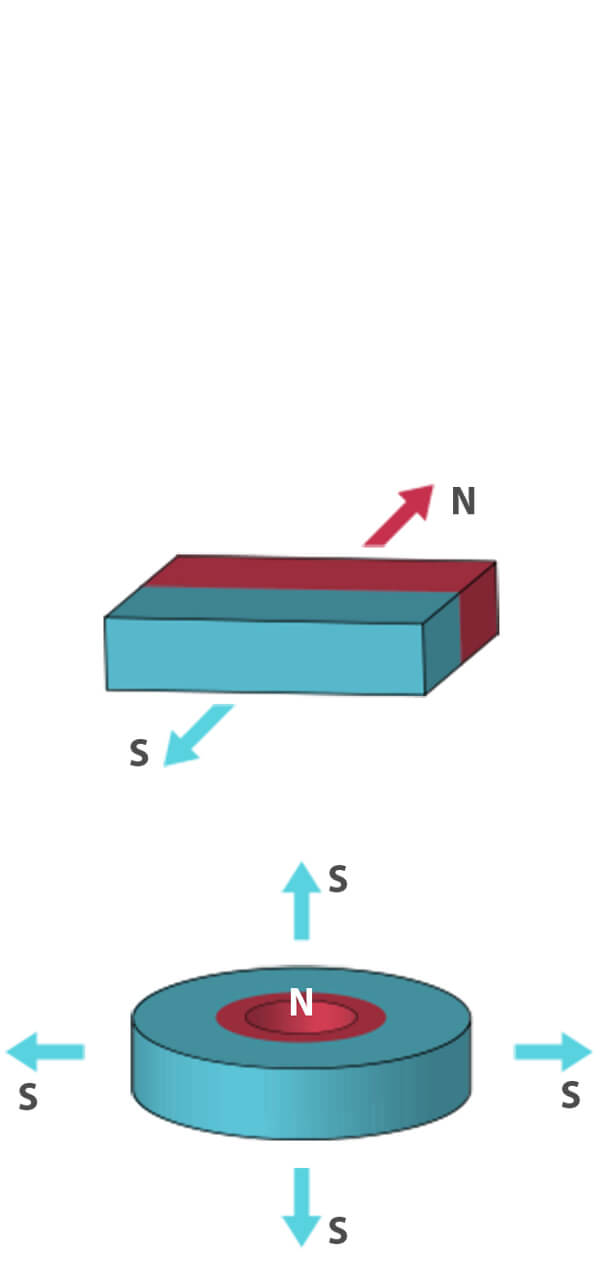
The magnetic field is an invisible stream extending between the ends of the magnet, and the stream itself is a collection of charged particles. Neodymium magnets have a potential energy characteristic, which means they have the ability to retain their own energy without losing it over the years, like batteries. Each magnet has two poles - north and south. This means that there are no magnets that have only one pole. It is worth noting that the poles are always located at opposite ends of the magnet.
Cylindrical Magnets - magnetization:
- axial - magnetization is along the height, meaning the magnet attracts most strongly with flat surfaces
- diametrical - magnetization is along the diameter, meaning the magnet attracts most strongly with the sides
- radial - magnetization is along the circumference, meaning the magnet attracts most strongly with the sides, with the outer and inner poles being uniform (either N or S) exclusively
Plate Magnets - magnetization:
- axial - magnetization signifies that the magnetic field runs parallel to the magnet's height, making its polar ends the primary points of attraction for flat surfaces.
- diametrical - magnetization is along the width, meaning the magnet attracts most strongly with the sides, which define the rectangle area with one dimension as the height and the other as the length of the magnet
- radial - magnetization is along the length, meaning the magnet attracts most strongly with the sides, which define the rectangle area with one dimension as the height and the other as the width of the magnet
Ring Magnets - magnetization:
- axial - magnetization occurs along the length of the magnet, which results in the magnet having the strongest attraction at its ends, perfectly suited for adhering to flat surfaces
- diametrical - magnetization is along the diameter, meaning the magnet attracts most strongly with the sides. This type of magnetization is not applied to ring magnets with a tapered hole
- radial - magnetization is along the circumference, meaning the magnet attracts most strongly with the sides, with the outer and inner poles being uniform (either N or S). This type of magnetization is not applied to ring magnets with a tapered hole
Neodymium reacts with oxygen and oxidizes very quickly if it is not protected (coated). That's why all neodymium magnets in our store are coated with a protective layer, which is so thin that it does not affect the adhesive force of the magnet while fulfilling its purpose. The protective coating also protects the magnet from scratches and chipping on the edges.
For surfaces such as nickel, gold, zinc, chrome, and epoxy resin, the magnet's force is the same because the protective layer is usually too thin to have an impact on the force. The layer of rubber or plastic is usually thicker and therefore partially reduces the magnet's force (increases the distance between the attracted object and the magnet).
There are several options for protective coatings of neodymium magnets. In our online store, we mainly offer nickel-plated magnets (the most popular), but you will also find some with a gold or silver coating or a polyepoxide surface. We can also produce magnets coated with rubber, plastic, zinc, or chrome for you - more information can be found in magnet production.
Nickel Coating (Ni-Cu-Ni)
- So far, the most commonly used coating
- Color: shiny metallic
- Good cost-to-performance ratio
- Thickness: approx. 12 micrometers
Gold Coating (Ni-Cu-Ni-Au)
- Gold plating (24k) over the regular Ni-Cu-Ni coating but with the same characteristics
- Color: shiny metallic
- Thickness of the gold layer without Ni-Cu-Ni: 0.05 micrometers
- Thickness of the entire coating: approx. 12 micrometers
Gold coating wears off easily with frequent use, making it suitable only for decorative purposes, not for play or work.
Chrome Coating (Ni-Cu-Ni-Cr)
- Best resistance to abrasion and pressure
- Color: gray metallic
- Thickness: approx. 15 micrometers
Copper Coating (Ni-Cu)
- Color: shiny bronze-red-gold. The color may change over time (darkening, spots)!
- Slightly weaker resistance to abrasion and impact compared to Ni-Cu-Ni
- Slightly weaker resistance to corrosion compared to Ni-Cu-Ni
- Thickness: approx. 10 micrometers
Copper coating is sometimes not visible to the naked eye, which is why (similarly to gold-plated magnets) it is not suitable for frequent use and is intended solely for decorative purposes.
Epoxy Resin Coating (Ni-Cu-Ni-Epoxy)
(also known as epoxy coating)
- Color: black
- Almost 100% corrosion-free if the coating is intact
- No shock resistance (crumbles quickly)
- Thickness: approx. 10 micrometers
Even the smallest damage to the coating, invisible to the naked eye, causes damage to the magnet, usually over a long period of exposure to moisture.
Nickel Rubber or Simply Rubber
- Color: black
- Very good impact resistance, rubber absorbs impact energy
- Rubber has a high friction coefficient: it is difficult to rub it against any surface, it stays in place
- Thickness: 0.5 to 2 millimeters
- Good chemical resistance
- The magnet is slightly weaker because the thicker rubber layer increases the distance between the magnet and the attracted object
Rubber protects the magnet from moisture.
Nickel-Plastic or Simply Plastic
- Color: other (colored)
- Similar to rubber, very good impact resistance
- Unlike rubber, the friction between plastic and other surfaces is lower
- Thickness: 0.5 to 2 millimeters
- Good chemical resistance
- The plastic layer increases the distance between the magnet and the attracted object, thereby slightly reducing the magnet's force
When properly sealed, it effectively limits the effects of moisture.
For our neodymium magnets, we offer not only nickel plating but also various types of coatings depending on your needs. In particular, our unique anti-corrosion coating technology significantly improves the corrosion resistance of neodymium magnets, with nickel being the standard. Please also consider other coating options when comparing them with plated products.
material | symbol | Coating Thickness (μm) | Corrosion Resistance (Salt Spray) (Hr) | Porosity | Demagnetization Rate | Color | PCT (Hr) |
---|---|---|---|---|---|---|---|
Zinc | Zn | 10-15 | >24 | <0.1 | <0.2% | White | >16 |
Colorful Zinc | Colorful-Zn | 10-15 | 72 | <0.1 | <0.1% | Multicolor | >24 |
Nickel | Ni | 10-20 | 4 | <0.5 | <0.3% | Silver | >16 |
Double Nickel | Double-Valued Ni | 15-20 | 24 | <0.2 | <0.3% | Silver | >16 |
Nickel-Copper-Nickel | Ni-Cu-Ni | 15-30 | >48 | <0.1 | <0.1% | Silver | >42 |
Zinc-Nickel Alloy | Zn-Ni Alloy | 10-20 | >720 | <0.1 | <0.1% | Various Colors | >72 |
Third-party Epoxy | Epoxy | 10-50 | >300 | - | - | Black | >24 |
Electroless Nickel | Electroless Ni | <1 | >72 | - | - | Silver | >24 |
Salt spray test: 37-39oC, 5% NaCl, pH 6.5-7.0, 1.5 ml/hr
PCT: 120oC, 2 atm, 100% RH, 12 hours
φ10mm×10mm |
Element symbolaa |
Element name |
Properties |
Usage |
---|---|---|---|---|
![]() |
3CrZn | Trivalent Chromium Zinc | Hexavalent chromium was recently classified as an environmentally hazardous substance and replaced with trivalent chromium. | Electronic parts, industrial tool parts |
![]() |
Ag | Silver | Silver has the best electrical conductivity of all metals, low contact resistance, and good solderability, but it tarnishes easily. | Electronic parts, Connectors, Dishes, Accessories |
![]() |
Au | Gold | Gold has good resistance to corrosion and oxidation and low electrical resistance. | Electronic parts, Electrical parts, Decorations, Accessories |
![]() |
Cr | Chromium | Chromium has good wear and oxidation resistance and does not lose its luster in the atmosphere. | External parts, Medical instruments, Audiovisual equipment, Accessories |
![]() |
Cu | Copper | Copper tarnishes easily, so it is used as a base. It is used to fill dents and provide shine. | Casting products, ABS resin base |
![]() |
CuZn | Bronze | Brass materials easily change color and are commonly used as a base layer. Brass is often used in ancient ornaments. | Ancient colorful ornaments |
![]() |
Ni | Nickel | Nickel is chemically stable and has good anti-corrosion properties. It can be used for various purposes and as a base for gold plating, chromium plating, etc. It may cause skin irritation. | Electronic parts, Connectors, Base coatings, Accessories |
![]() |
NiBlack | Black Nickel | Black nickel is an alloy coating made of nickel, zinc, and sulfur. The color may vary depending on the type of base coating used. | Decorations, Accessories |
![]() |
Sn | Tin | Tin has excellent anti-corrosion properties and does not oxidize easily. It retains its luster and can be safely used in food products. | Food containers, Cans, Tin items, Decorations, Accessories |
![]() |
Rh | Rhodium | Rhodium has excellent anti-corrosion properties and does not oxidize easily. It retains its luster and can be safely used in food products. | Electronic parts, Electrical parts, Audio parts, Decorations, Accessories |
![]() |
- | Untreated | No surface treatment coating. Rust will easily develop on neodymium magnets. | |
![]() |
- | Nylon | Made without organic solvents and used in food processors and medical devices. Passed the Food Hygiene Law. | Toys, Small articles |
![]() |
- | Polyamide MF305 | High impact resistance, bending resistance, and applicability at high temperatures. | Electronic parts, Small articles, Post-paint bending |
- | - | Epoxy MF304 | High resin hardness / Flame retardancy regulation: UL94 / V-0 Certified | Electronic parts, Small articles |
- | - | Epoxy MF303 | High resin hardness / Easy to polish | Decorations |
Dhit | Company [S] | Other companies | Dhit | Company [T] | Dhit | |
---|---|---|---|---|---|---|
Duration | HDC Coating, Epoxy Resin, MF304 | Normal epoxy resin | Anti-corrosion primer Zn for car Zn | HDC, Epoxy Resin Coating, MF305 | Epoxy resin | NiCuNi, 3 layers, nickel |
Before the test |
![]() |
|||||
After 72 hours |
![]() |
|||||
After 312 hours |
![]() |
|||||
After 504 hours |
![]() |
Salt spray test: 37-39oC, 5% NaCl, pH 6.5-7.0, 1.5 ml/hr
PCT: 120oC, 2 atm, 100% RH, 12 hours
Depending on the temperature, there are three different types of losses:
- reversible (can be reversed)
- irreversible (cannot be reversed)
- constant
Reversible Loss of Magnetization
- Temperature range: slightly above the maximum operating temperature
- Temperature range: slightly above the maximum operating temperature
- The magnet is less magnetic when hot
- It doesn't matter how often the magnet is heated and cooled
Irreversible Loss
- Temperature range: significantly above the maximum operating temperature
- The magnet is permanently weakened, even after cooling
- Repeated heating at the same temperature does not strengthen irreversible losses
- Magnetization of an irreversibly weakened magnet by a sufficiently strong external magnetic field can restore its original strength
Constant Loss of Magnetic Properties
The structure of neodymium magnets changes due to high temperature - magnetization is no longer possible
shape | sketch | parameters | ||||
---|---|---|---|---|---|---|
cylindrical magnet |
![]() |
dimension | ||||
D(mm) | L(mm) | magnetization direction | ||||
all grades | 1.0 ~ 250 mm | ≤ 80 mm | axial or radial | |||
ring magnet |
![]() |
dimension | ||||
D(mm) | P(mm) | L(mm) | magnetization direction | |||
all grades | 2.5 ~ 250 mm | 0.8 ~ 230 mm | ≤ 80 mm | ≤ 80 mm | ||
block magnet |
![]() |
dimension | ||||
L(mm) | W(mm) | H(mm) | magnetization direction | |||
all grades | ≤ 200 mm | ≤ 100 mm | ≤ 80 mm | ≤ 80 mm | ||
segment |
![]() |
dimension | ||||
H(mm) | W(mm) | L(mm) | magnetization direction | |||
all grades | ≤ 70 mm | ≤ 100 mm | ≤ 200 mm | ≤ 80 mm |
material | strength % |
---|---|
Carbon steel 0.1 - 0.3 % C | 100 |
Carbon steel 0.4 - 0.5 % C | 90 |
Alloy steel F-522 | 80-90 |
Cast iron | 45-60 |
Stainless steel 18% chromium and 8% nickel | 0 |
Brass aluminum copper | 0 |
type | max. operating temperature | Curie temperature | Thermal expansion coefficient | Thermal conductivity |
---|---|---|---|---|
N* | 80°C (176°F) | 310°C (590°F) | -0.12%/°C | 7.7 kcal/m-h-°C |
M | 100°C (212°F) | 340°C (644°F) | -0.12%/°C | 7.7 kcal/m-h-°C |
H | 120°C (248°F) | 340°C (644°F) | -0.11%/°C | 7.7 kcal/m-h-°C |
SH | 150°C (302°F) | 340°C (644°F) | -0.10%/°C | 7.7 kcal/m-h-°C |
UH | 180°C (356°F) | 350°C (662°F) | -0.10%/°C | 7.7 kcal/m-h-°C |
EH | 200°C (392°F) | 350°C (662°F) | -0.10%/°C | 7.7 kcal/m-h-°C |
AH | 230°C (446°F) | 350°C (662°F) | -0.10%/°C | 7.7 kcal/m-h-°C |
* The maximum operating temperatures in this table are reference points only. Magnets with the N52 grade have a maximum operating temperature of 65 °C.
For applications with neodymium magnets at temperatures above 80 °C, we offer a special type of magnet with a higher operating temperature in our range.
properties | units | values |
---|---|---|
Vickers hardness | Hv | ≥550 |
Density | g/cm3 | ≥7.4 |
Curie Temperature TC | °C | 312 - 380 |
Curie Temperature TF | °F | 593 - 716 |
Specific resistance | μΩ⋅Cm | 150 |
Bending strength | Mpa | 250 |
Compressive strength | Mpa | 1000~1100 |
Thermal expansion parallel (∥) to orientation (M) | °C-1 | (3-4) x 106 |
Thermal expansion perpendicular (⊥) to orientation (M) | °C-1 | -(1-3) x 10-6 |
Young's modulus | kg/mm2 | 1.7 x 104 |
Material type | Remanence | Coercivity | Intrinsic coercivity | Energy density | Operating temperature | ||||
---|---|---|---|---|---|---|---|---|---|
Br(kGs) | Br(T) | (BH)max(MGOe) | (BH)max(KJ/m) | ||||||
Min. - Max. | Min. - Max. | bHc(kOe) | bHc(kA/m) | iHc(kOe) | iHc(kA/m) | Min. - Max. | Min. - Max. | ||
N30 | 10.8-11.2 | 1080-1120 | 9.8-10.5 | 780-836 | ≥12 | ≥955 | 28-30 | 223-239 | ≤ 80°C |
N33 | 11.4-11.7 | 1140-1170 | 10.3-11 | 820-876 | ≥12 | ≥955 | 31-33 | 247-263 | ≤ 80°C |
N35 | 11.7-12.1 | 1170-1210 | 10.8-11.5 | 860-915 | ≥12 | ≥955 | 33-35 | 263-279 | ≤ 80°C |
N38 | 12.2-12.6 | 1220-1260 | 10.8-11.5 | 860-915 | ≥12 | ≥955 | 36-38 | 287-303 | ≤ 80°C |
N40 | 12.6-12.9 | 1260-1290 | 10.5-12.0 | 860-955 | ≥12 | ≥955 | 38-40 | 303-318 | ≤ 80°C |
N42 | 12.9-13.2 | 1290-1320 | 10.8-12.0 | 860-955 | ≥12 | ≥955 | 40-42 | 318-334 | ≤ 80°C |
N45 | 13.2-13.7 | 1320-1370 | 10.8-12.5 | 860-995 | ≥12 | ≥955 | 43-45 | 342-358 | ≤ 80°C |
N48 | 13.7-14.2 | 1370-1420 | 10.8-12.5 | 860-995 | ≥12 | ≥955 | 45-48 | 358-382 | ≤ 80°C |
N50 | 14-14.6 | 1400-1460 | 10.8-12.5 | 860-995 | ≥12 | ≥955 | 47-51 | 374-406 | ≤ 80°C |
N52 | 14.2-14.7 | 1420-1470 | 10.8-12.5 | 860-995 | ≥12 | ≥955 | 48-53 | 380-422 | ≤ 65°C |
N54 | 14.5-15.1 | 1450-1510 | 10.8-12.5 | 860-995 | ≥12 | ≥876 | 51-55 | 406-438 | ≤ 80°C |
N30M | 10.8-11.2 | 1080-1120 | 9.8-10.5 | 780-836 | ≥14 | ≥1114 | 28-30 | 223-239 | ≤100°C |
N33M | 11.4-11.7 | 1140-1170 | 10.3-11 | 820-876 | ≥14 | ≥1114 | 31-33 | 247-263 | ≤100°C |
N35M | 11.7-12.1 | 1170-1210 | 10.8-11.5 | 860-915 | ≥14 | ≥1114 | 33-35 | 263-279 | ≤100°C |
N38M | 12.2-12.6 | 1120-1260 | 10.8-11.5 | 860-915 | ≥14 | ≥1114 | 36-38 | 287-303 | ≤100°C |
N40M | 12.6-12.9 | 1260-1290 | 10.8-12 | 860-955 | ≥14 | ≥1114 | 38-40 | 303-318 | ≤100°C |
N42M | 12.9-13.2 | 1290-1320 | 10.8-12.5 | 860-995 | ≥14 | ≥1114 | 40-42 | 318-334 | ≤100°C |
N45M | 13.2-13.7 | 1320-1370 | 10.8-13 | 860-1035 | ≥14 | ≥1114 | 43-45 | 342-358 | ≤100°C |
N48M | 13.7-14.2 | 1370-1420 | 10.8-12.5 | 860-995 | ≥14 | ≥1114 | 45-48 | 358-382 | ≤100°C |
N50M | 14-14.6 | 1400-1460 | 10.8-12.5 | 860-995 | ≥14 | ≥1114 | 47-51 | 374-406 | ≤100°C |
N27H | 10.2-10.6 | 1020-1060 | 9.5-10.1 | 756-804 | ≥17 | ≥1353 | 25-27 | 199-215 | ≤120°C |
N30H | 10.8-11.2 | 1080-1120 | 10.1-10.6 | 804-844 | ≥17 | ≥1353 | 28-30 | 223-239 | ≤120°C |
N33H | 11.4-11.7 | 1140-1170 | 10.3-11 | 820-876 | ≥17 | ≥1353 | 31-33 | 247-263 | ≤120°C |
N35H | 11.7-12.1 | 1170-1210 | 10.8-11.5 | 860-915 | ≥17 | ≥1353 | 33-35 | 263-279 | ≤120°C |
N38H | 12.2-12.6 | 1120-1260 | 10.8-11.5 | 860-915 | ≥17 | ≥1353 | 36-38 | 287-303 | ≤120°C |
N40H | 12.6-12.9 | 1260-1290 | 10.8-12 | 860-955 | ≥17 | ≥1353 | 38-40 | 303-318 | ≤120°C |
N42H | 12.9-13.2 | 1290-1320 | 10.8-12 | 860-955 | ≥17 | ≥1353 | 40-42 | 318-334 | ≤120°C |
N44H | 13.2-13.6 | 1320-1360 | 10.8-13 | 860-1035 | ≥17 | ≥1353 | 42-44 | 334-350 | ≤120°C |
N48H | 13.7-14.2 | 1370-1420 | 10.8-12.5 | 860-995 | ≥17 | ≥1353 | 45-48 | 358-382 | ≤120°C |
N27SH | 10.2-10.6 | 1020-1060 | 9.5-10.1 | 756-804 | ≥20 | ≥1592 | 25-27 | 199-215 | ≤150°C |
N30SH | 10.8-11.2 | 1080-1120 | 10.1-10.6 | 804-844 | ≥20 | ≥1592 | 28-30 | 223-239 | ≤150°C |
N33SH | 11.4-11.7 | 1140-1170 | 10.3-11 | 820-876 | ≥20 | ≥1592 | 31-33 | 247-263 | ≤150°C |
N35SH | 11.7-12.1 | 1170-1210 | 10.8-11.5 | 860-915 | ≥20 | ≥1592 | 33-35 | 263-279 | ≤150°C |
N38SH | 12.2-12.6 | 1120-1260 | 10.8-11.5 | 860-915 | ≥20 | ≥1592 | 36-38 | 287-303 | ≤150°C |
N40SH | 12.6-12.9 | 1260-1290 | 10.8-12.0 | 860-955 | ≥20 | ≥1592 | 38-40 | 303-318 | ≤150°C |
N42SH | 12.9-13.2 | 1290-1320 | 10.8-12 | 860-955 | ≥20 | ≥1592 | 40-42 | 318-334 | ≤150°C |
N45SH | 13.2-13.7 | 1320-1370 | 10.8-12.5 | 860-955 | ≥20 | ≥1592 | 43-45 | 342-358 | ≤150°C |
N25UH | 9.8-10.2 | 980-1020 | 9.2-9.6 | 732-764 | ≥25 | ≥1990 | 23-25 | 183-199 | ≤180°C |
N28UH | 10.4-10.8 | 1040-1080 | 9.8-10.2 | 780-812 | ≥25 | ≥1990 | 26-28 | 207-233 | ≤180°C |
N30UH | 10.8-11.2 | 1080-1120 | 10.1-10.6 | 804-844 | ≥25 | ≥1990 | 28-30 | 223-239 | ≤180°C |
N33UH | 11.4-11.7 | 1140-1170 | 10.3-11 | 820-876 | ≥25 | ≥1990 | 31-33 | 247-263 | ≤180°C |
N35UH | 11.7-12.1 | 1170-1210 | 10.8-11.5 | 860-915 | ≥25 | ≥1990 | 33-35 | 263-279 | ≤180°C |
N38UH | 12.2-12.6 | 1120-1260 | 10.8-11.5 | 860-915 | ≥25 | ≥1990 | 36-38 | 287-303 | ≤180°C |
N40UH | 12.6-12.9 | 1260-1290 | 10.5-12.0 | 860-955 | ≥25 | ≥1990 | 38-40 | 303-318 | ≤180°C |
N25EH | 9.8-10.2 | 980-1020 | 9.2-9.6 | 732-764 | ≥30 | ≥2388 | 23-25 | 183-199 | ≤200°C |
N28EH | 10.4-10.8 | 1040-1080 | 9.8-10.2 | 780-812 | ≥30 | ≥2388 | 26-28 | 207-223 | ≤200°C |
N30EH | 10.8-11.2 | 1080-1120 | 10.1-10.6 | 804-844 | ≥30 | ≥2388 | 28-30 | 223-239 | ≤200°C |
N33EH | 11.4-11.7 | 1140-1170 | 10.3-11 | 820-876 | ≥30 | ≥2388 | 31-33 | 247-263 | ≤200°C |
N35EH | 11.7-12.1 | 1170-1210 | 10.8-11.5 | 860-915 | ≥30 | ≥2388 | 33-35 | 263-279 | ≤200°C |
N38EH | 12.2-12.5 | 1120-1250 | ≥11.3 | ≥899 | ≥30 | ≥2388 | 36-39 | 287-310 | ≤200°C |
N40EH | 12.5-12.8 | 1250-1280 | ≥11.6 | ≥923 | ≥30 | ≥2388 | 38-41 | 302-326 | ≤200°C |
N42EH | 12.8-13.2 | 1280-1320 | ≥11.7 | ≥931 | ≥30 | ≥2388 | 40-43 | 318-342 | ≤200°C |
N28AH | 10.4-10.8 | 1040-1080 | ≥9.9 | ≥787 | ≥33 | ≥2624 | 26-29 | 207-231 | ≤230°C |
N30AH | 10.8-11.3 | 1080-1130 | ≥10.3 | ≥819 | ≥33 | ≥2624 | 28-31 | 223-247 | ≤230°C |
N33AH | 11.3-11.7 | 1130-1170 | ≥10.6 | ≥843 | ≥33 | ≥2624 | 31-34 | 247-271 | ≤230°C |
N35AH | 11.7-12.2 | 1170-1120 | ≥11.0 | ≥876 | ≥33 | ≥2624 | 33-36 | 263-287 | ≤230°C |
N38AH | 12.2-12.5 | 1120-1250 | ≥11.3 | ≥899 | ≥33 | ≥2624 | 36-39 | 287-310 | ≤230°C |
N40AH | 12.5-12.8 | 1250-1280 | ≥11.6 | ≥923 | ≥33 | ≥2624 | 38-41 | 302-326 | ≤230°C |
The table below provides information on the Maximum Operating Temperature and Curie Temperature for various N Grades. Understanding these parameters is particularly important when selecting a magnet for applications in elevated temperature conditions.
type/grade of magnet | maximum operating temperature | Curie temperature |
---|---|---|
N | 80°C / 176°F | 310°C / 590°F |
NM | 100°C / 212°F | 340°C / 644°F |
NH | 120°C / 248°F | 340°C / 644°F |
NSH | 150°C / 302°F | 340°C / 644°F |
NUH | 180°C / 356°F | 350°C / 662°F |
NEH | 200°C / 392°F | 350°C / 662°F |
NAH | 230°C / 446°F | 350°C / 662°F |
Neodymium Magnets Production Technology is the process of creating high-strength magnets from neodymium, iron, and boron. This process involves several steps, including raw material preparation, pressing, granulation, shaping, hardening, and magnetization. Depending on the product requirements, different magnetization methods can be employed, such as direct current or pulsed magnetization. Due to their exceptional properties, neodymium magnets are widely used in various industries, including automotive, electronics, medical, and energy.