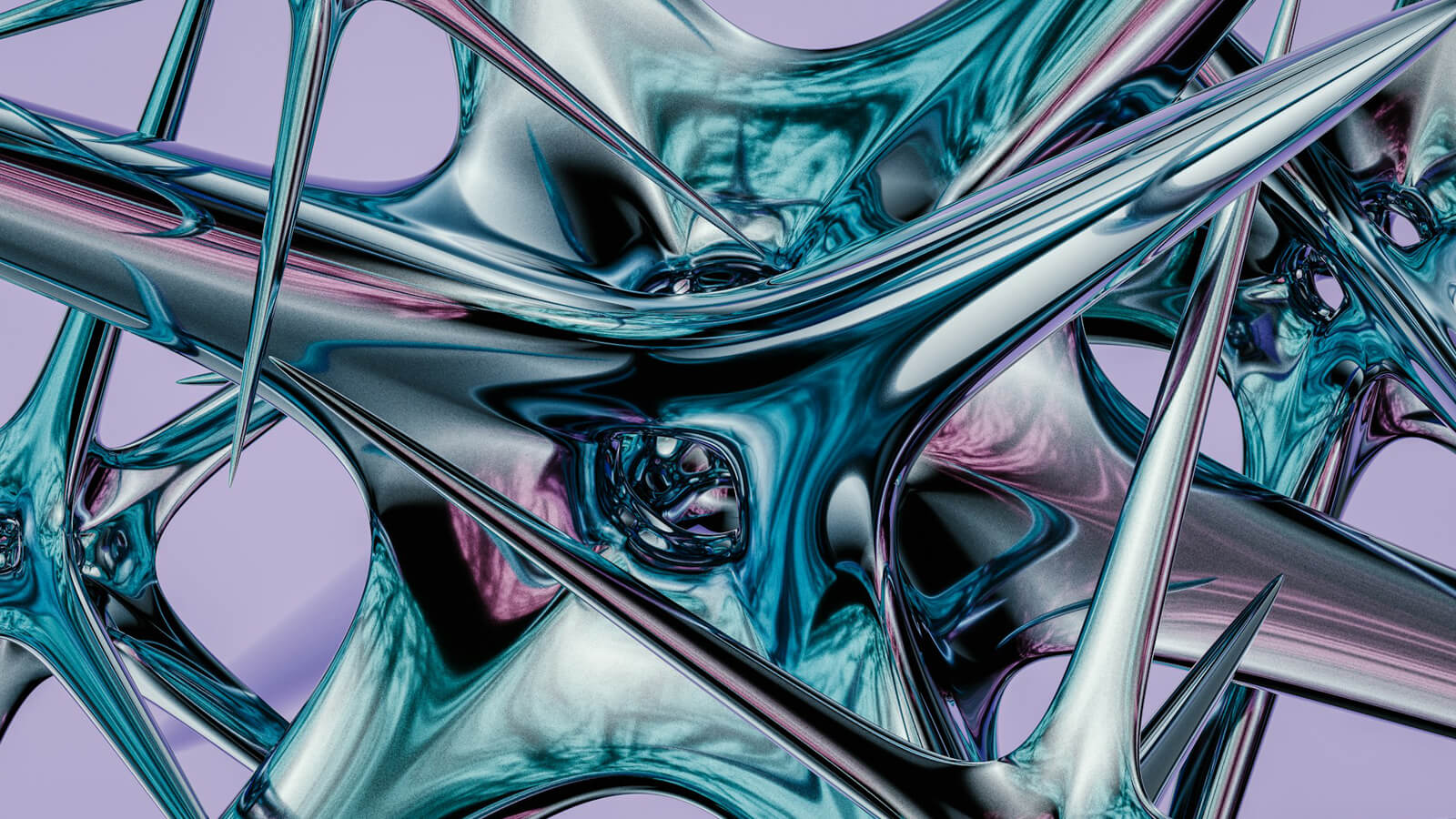
Why is coating so important?
Neodymium magnets are among the most powerful magnetic materials in the world. However, without a suitable coating, they oxidize rapidly, which decreases their magnetic strength and longevity. In this article, we will examine various coatings that protect magnets from moisture, high temperatures, chemical substances, and mechanical damage.
Most popular types of coatings
Below is an overview of the most frequently encountered coatings on neodymium magnets – from classic nickel to Teflon and specialized polymers.
Nickel (Ni-Cu-Ni): The most commonly used coating, usually triple-layered (nickel–copper–nickel). It provides good corrosion protection in moderately humid conditions.
Electroless nickel: Similar to standard nickel but significantly more resistant to alkalis, acids, and saline solutions.
Plastic: A thicker layer that shields the magnet from impacts and corrosion. It is waterproof but slightly diminishes the pulling force.
Epoxy (Ni-Cu-Ni-Epoxy): An extra layer over nickel, typically black in color. It provides excellent protection but is prone to scratching.
Zinc: An economical solution, which upon oxidation forms a layer of zinc oxide that further protects against corrosion.
Gold (24k): A thin layer applied over nickel, often used in magnet therapy or for aesthetic reasons.
Silver: Popular in medical applications due to its biocompatibility and resistance to bacteria.
Everlube®: A highly durable aluminized coating that stands up to chemicals and corrosion in a wide range of conditions.
Teflon® (PTFE) / Xylan®: Outstanding chemical and corrosion resistance, but poor adhesion for glues.
Parylene: An ultrathin coating providing the highest tightness and abrasion resistance, frequently used in medical or aerospace industries.
How to select the right coating?
Choosing the right coating mainly depends on the environment in which the magnet will function. If the magnet is in contact with water or chemicals, Teflon, plastic, or electroless nickel is a good option. If appearance or aesthetic features (for example, in magnet therapy) are your priority, a gold or silver coating could be ideal.
When in doubt, it is advisable to consult a specialist who can help pick the most suitable option. The proper coating will extend the magnet's lifespan by protecting it from external factors and preventing a loss of magnetic strength.
Summary
Neodymium magnets require appropriate protection to maintain their full potential and avoid corrosion. Various coatings—from nickel and epoxy to plastics and advanced parylene—let you tailor the degree of protection to specific applications. Bear in mind that each coating can impact the magnet's final parameters, such as pulling force or mechanical durability.
If you want to learn more about magnet technology and production, check out our technology section: find out more about the magnet manufacturing process.
Tags:
#coatings#neodymium magnets#anti-corrosion protectionponiedziałek 2025-02-03T18:00:00